#GRATENEWS
August 2021 Update
Wyndham City Council officially approves SMC Ecolite pit lids as conforming to AS3996:2019!
Explore the new composite lid testing requirements of AS3996:2019.
Wyndham City Council officially approves SMC Ecolite pit lids as conforming to AS3996:2019!
We’re delighted to confirm that Wyndham City Council has approved the use of R&S Grating’s SMC Ecolite pit lids within its municipality, finding that SMC Ecolites passed the required tests of AS3996:2019 and therefore conformed to the standard.
With the release of the revised standard AS3996:2019 Access Covers & Grates came enhanced testing and performance requirements for polymeric material access covers. Wyndham City Council took the opportunity to evaluate composite lids for conformance to the standard and are to be commended for ensuring that products used within their council conform to the high levels specified in AS3996:2019. Non-conforming products remain a serious issue for councils, with many non-conforming products not just failing the requirements of AS3996:2019, but posing serious safety concerns for the community.
The enhanced testing of AS3996:2019 was intended to simulate the real-life experiences of composite material lids. As composite materials behave very differently to the traditional materials covered by AS3996, in particular steel and iron, new tests were introduced that are uniquely tailored to composite materials and ensure the longevity of products and ongoing community safety.
As an industry leader in composite lids, R&S Grating has long championed better guidance and stricter conformance requirements. Having supplied the first full-depth composite lid in the market, we were pleased that the Standard committee saw fit to adopt the requirement of full-depth composite materials and ban the use of timber and other material in the construction of conforming lids. Enhanced testing requirements will ensure that as the prevalence of composite lids continues to grow, local councils can rest assured that conforming products are designed to pass the most important test of all, the test of time.
Explore the enhanced tests of AS3996:2019 and the results for R&S Grating’s SMC Ecolite pit lids below or get in touch for a full copy of the test results.
Ultraviolet Testing
Why is ultraviolet testing needed?
Ultraviolet testing was introduced to AS3996 in the 2019 release for the first time. While Australia has long felt the effects of harsher ultraviolet radiation than other parts of the world, grates and access covers have typically been made of steel, iron or concrete, which are not prone to degradation from ultraviolet radiation. Unlike these materials, plastics in their many forms, including sheet moulded compound (SMC) and fibreglass reinforced plastic (FRP), are prone to material degradation from prolonged ultraviolet exposure. The strength and performance of a composite lid will be compromised after UV degradation has occurred. In some instances, the lid may still function, however UV damage can also lead to the catastrophic failure of composite lids, with damaged material unable to sustain simple loads, cracking or even full collapse.
How does ultraviolet radiation damage composite materials?
Ultraviolet radiation degrades composite materials in a variety of ways, but most critically it breaks the polymer chains, causes free radicals and reduces the molecular weight of the material. This degradation is similar to the process that causes many biological cancers as a result of prolonged UV exposure. R&S Grating’s SMC Ecolite pit lids have a distinct advantage over biological material and inferior composite materials, in that a variety of compounds are added to the sheet moulded compound material that act to absorb UV radiation, block UV radiation and stabilise the material. These compounds ensure that even after prolonged UV exposure the strength and performance of the material are not compromised. In addition to the compound additives, R&S Grating’s SMC ecolite pit lids include a UV-resistant paint coating, adding an additional layer of protection.
How do we test composite materials for ultraviolet resistance?
AS3996:2019 requires that polymeric materials used in the construction of grates and covers be stabilised such that prolonged UV exposure will not compromise the product for a minimum of 25 years. To test this, “dumbbell” sections are cut from the material. Half of these dumbbells have their tensile modulus tested without prolonged UV exposure. The remainder are then subjected to prolonged UV exposure by one of two methods specified in AS3996:2019.
The SMC Ecolite material was subjected to fluorescent UV lamp exposure as specified in ISO 4892-3:2016 for a duration of 1800 hours (75 days). After this exposure, the tensile modulus is measured using the exposed samples. AS3996:2019 requires a change in the tensile modulus of less than 20% between the exposed and non-exposed samples. The SMC Ecolite material had a change of tensile modulus of 14.8% after exposure, not only passing the test, but demonstrating the advantage and success of the UV-resistant compound additives used in SMC Ecolites.
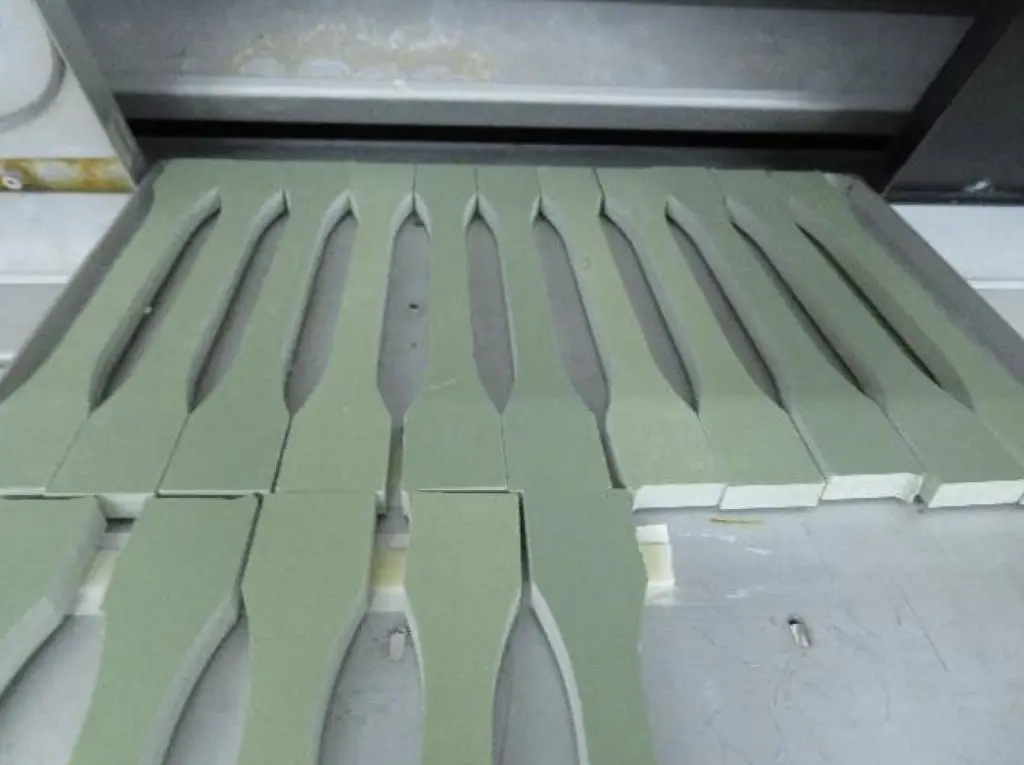
Impact Resistance Testing
Why is impact resistance testing important?
In real-world applications, light-weight composite lids are likely to experience a variety of impact events over time. These may include heavier items being dropped, unexpected or unusual vehicle loading and any manner of event that might apply a sudden, impact load to the cover.
It is important to note that these impact events are not the typical anticipated loading, for example a car tyre traversing the cover. This type of loading is assessed by the standard type tests specified in AS3996:2019 that apply to all products covered by the standard. Impact resistance is tailored to composite covers and grates, with the plasticity of the composite material making it more prone to damage from sudden impact events.
To ensure that covers and grates are adequately designed to withstand these events, AS3996:2019 includes the requirement of impact resistance testing.
How do we test composite lids for impact resistance?
AS3996:2019 introduced impact resistance testing to assess covers and grates. The test is conducted by using a solid steel “striker” that is dropped down a smooth guide pipe from a height of 2.5m. The mass of the striker required is determined by the class rating being tested. In the case of class B, this is 3.75kg.
The test must be conducted at the weakest point of the cover, as well as at an additional four points. The depth of indentations must be measured and not exceed 5mm. Additionally, the grate or cover must not crack on the top or bottom.
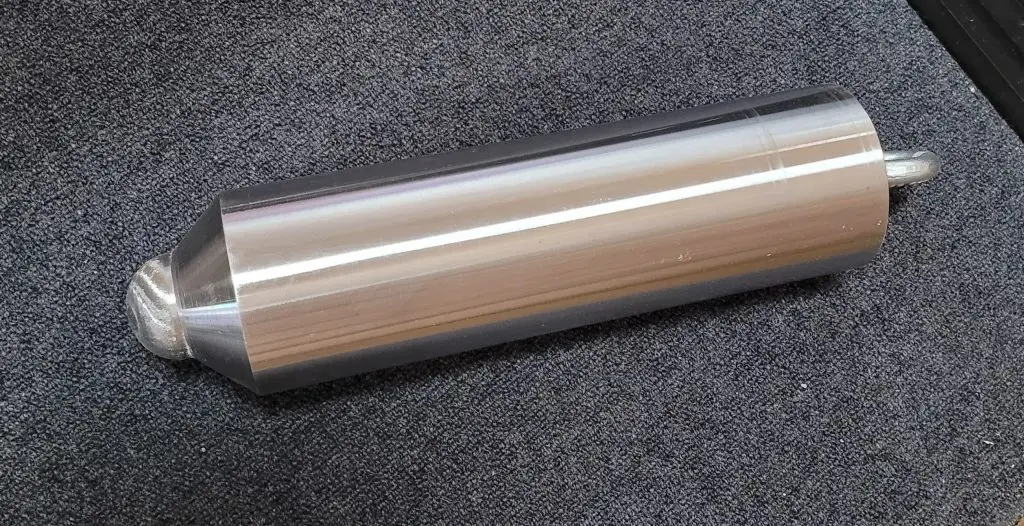
The test must be conducted in ambient conditions, with the cover conditioned to a temperature of 15°C–25°C, with the cover or grate secured in position and the guide pipe located a minimum of 30mm from the cover.
The SMC Ecolite was assessed to pass the impact resistance test, with an indentation of 1.2mm at the weakest point and indentations of 0.8mm, 0.9mm, 0.3mm and 0.6mm at the other four positions tested.
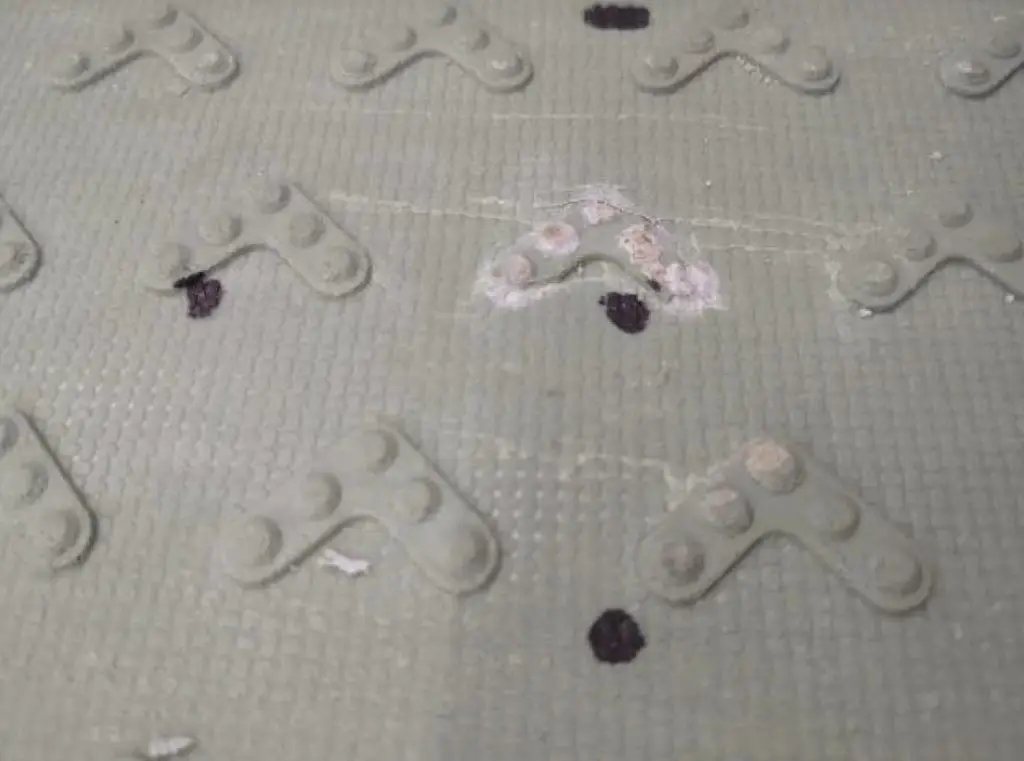
Creep Resistance Testing
What is creep resistance?
Creep is the tendency for material to deform under a sustained or persistent load as opposed to a sudden or short-term load. Such loading may occur if a cover or grate has a vehicle parked on it for an extended time, a piece of machinery may also be placed on the cover or grate, or any other loading that can be considered extended. Under these sustained loads, composite materials may deflect and distort in different manners to how they would behave under the same load but applied for a shorter time. For this reason, AS3996:2019 requires creep resistance testing.
How is creep resistance tested?
AS3996:2019 includes creep resistance testing requirements, using the serviceability design load (53kN for class B), with the requirement that the load be applied for 24 hours. The test must be conducted with the cover or grate at a temperature of 18°C–25°C. Unlike other load tests of AS3996:2019, which require that the test be conducted at the weakest point, the creep is a property of the material, not the design, and so it is conducted at the geometric centre of the cover or grate.
After the load has been applied for 24 hours and released, the creep is measured as the difference between the deflection before the load was applied and after the load has been removed. The criteria to pass the test is a creep of less than 1 in 100 of the circular opening size.
The SMC Ecolite recorded a creep of 1.0mm, with a permissible creep of 6.97mm, demonstrating that even under sustained loads SMC Ecolite lids will return to within 1 in 100 of its original form.
Slip Resistance Testing
Why is slip resistance important?
Understandably, it is essential that covers and grates are not slippery when wet, or even oily. This slip-resistance is not just for the obvious scenario of someone walking on a grate or cover but extends more broadly in AS3996:2019 to cover all manner of scenario where the ability of a grate or cover to provide resistance from slipping may be useful, such as car tyres when braking. In the case of composite lids, however, the primary focus remains the safety of the community while traversing a composite lid. Many composite lids are installed in nature strips and areas where pedestrians are more likely to be found than vehicles, meaning it is essential that slip-resistance is factored into the design of the composite lid.
How is slip resistance tested?
The measurement of a surface’s ability to resist slipping is in no way unique to grates and covers and many different testing methods are available to make an assessment. Two of the most popular testing methods in Australia are the oil-wet ramp slip resistance test and the wet pendulum test (AS4586).
AS3996:2019 standardised slip-resistance testing for the industry by specifying the use of the wet pendulum test to determine a cover or grate’s slip resistance.
The wet pendulum test works by swinging a pendulum that is allowed to make contact with the surface and then the height that the pendulum reaches after contact is measured. AS3996:2019 requires a result of P3, P4 or P5 in the test. P3 is a value between 35-44, P4 is a value between 45-54 and P5 is value greater than 55. A zero value on this scale corresponds to the pendulum swinging parallel to the ground or surface. Essentially, the higher the value, the higher the slip resistance. The SMC Ecolite surface achieves an SRV of 78, giving it a rating of P5, or very good slip resistance.